فهرست مطالب
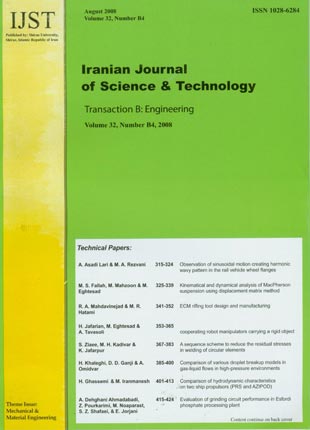
Iranian Journal of science and Technology (B: Engineering)
Volume:32 Issue: 4, August 2008
- Mechanical & Materials Engineering
- 122 صفحه،
- تاریخ انتشار: 1387/06/15
- تعداد عناوین: 9
-
-
Pages 315-324Railway wheels are subject to kinematic oscillation and forces (normal and tangential) which are time and location dependent. The forgoing is due to a transverse slope in the tread region and the forces are functions of the vehicle weight, the suspension and braking systems, track topography and irregularities, and the wheel/rail profiles. As a result, a variety of patterns are generated in the wheel surface. An investigation in Iranian Railways was launched to determine the reasons for the high wheel wear rate of rail vehicles which often cause an asymmetric pattern within a wheelset. Therefore, for the purposes of this research two test bogies were marked and equipped with the apparatus for the further measurement of wheel wear. A development of circumferential pattern, for the first time, was observed in the flange region of wheel surfaces acquired by measured patterns created on the test bogies’ wheels. Theoretical aspects of this harmonic pattern are developed and presented in this paper.
-
Pages 325-339In this paper, kinematics and dynamics of the MacPherson suspension are studied. Displacement Matrix Method is utilized for this purpose. Camber and toe angle alterations are derived by means of the rotation matrix. Kinematical characteristics of the MacPherson suspension are displayed as functions of time and the wheel vertical displacement. Relations for velocities and accelerations of key points are also obtained. Since internal forces and external forces are important in stress analysis and for comfortability, these forces are calculated as functions of time as well. Subsequently, a general analysis of the mechanism under the wheel sinusoidal displacement is presented together with relevant figures and results.
-
ECM rifling tool design and manufacturingPages 341-352Electrochemical rifling is one of the most effective and well-known methods for barrel rifling in the inner surface of complex shapes. In this research a desirable rifling tool is designed, modeled and manufactured via electrochemical theories. Then the manufactured tool electrode is tested and the theoretical and experimental results are compared with each other. This comparison shows a very good agreement, confirming that the desired processes can be theoretically analyzed via electrochemical basic theories on one hand, and also effective machining parameters determination on the other. This method can easily replace the high cost trial and error methods commonly in practice.
-
Pages 353-365In this paper, dynamic modeling and neural network control of two cooperating 6 DOF elbow manipulators handling a rigid object are studied when actuator dynamics is considered as an important part of the system dynamics. First, a kinematic model of the system and the relations between various forces/torques acting on the object by using different Jacobians, and also the dynamics of the mechanical subsystem are derived. Then, the actuator dynamics of each robot is included in the dynamic equations of the robotic system and a third order matrix equation is obtained. Finally, a neural network control scheme is developed for this third order dynamics and an appropriate Lyapunov function is established. The proposed controller guarantees asymptotic behavior for tracking the object desired trajectory. Numerical simulation of the cooperating robotic system in the presence of uncertainties is provided to demonstrate the robust performance of the proposed control scheme.
-
Pages 367-383Accurately predicting welding residual stresses and developing a convenient welding sequence for a weld system is an appropriate task since welding residual stress is inevitably produced in a welded structure. In this work, the effect of layered, block and cascade welding sequences on the thermo-mechanical response of shell weldments is studied by use of a 3-D thermo-viscoplastic model. An Anand model is used to simulate the rate dependent plastic deformation of welded materials. At the same time, modeling of the welded region in the present study has been done on the basis of the "isothermal melting pool" approach. The temperature dependency of the thermal and mechanical properties of materials is considered in the analysis and the effect of the welding speed and welding lag, and the inter-pass temperature is introduced into the model as well. Thus, the model presented here has provided a convenient welding sequence to enhance the fabrication process of a circular weld.
-
Pages 385-400Droplet breakup affects spray penetration and evaporation, and plays a critical role in engine efficiency. The purpose of this research was to examine the rate of penetration and evaporation of droplets in a combustion chamber, and the efficiency of the engine when liquid jet is injected into the compressed gas chamber in an axi-symmetrical fashion leading to a turbulent and unsteady flow. As a result of interaction with the highly compressed air in the chamber, the liquid jet breaks up and forms minute droplets. These particles will in turn breakup because of aerodynamic forces, producing even smaller droplets. A number of models are available for analyzing the breakup of droplets; however, each model is typically reliable only over a limited parameter range. In this research three well-known models are applied for droplet breakup modeling and their results are compared. To obtain the details of the flow field, the Eulerian gas phase mass, momentum and energy conservation equations, as well as equations governing the transport of turbulence and fuel vapor mass fraction are solved together with equations of trajectory, momentum, mass and energy conservation for liquid droplets in Lagrangian form. The numerical solution is performed using the finite volume method and EPISO (Engine-PISO) algorithm. The results obtained from the models show that the breakup process in a high pressure environment significantly affects the penetration and evaporation rates of the spray, and the droplet size is determined by the balance between breakup and coalescence processes. It is also shown that the details of atomization in the nozzle do not significantly influence the ultimate size of droplets. It should be mentioned that droplet collision modeling has been taken into account in the computer code and is activated wherever necessary.
-
Pages 401-413This paper presents a comparison of the hydrodynamic characteristics of two ship propulsors, a conventional system that is a propeller-rudder system (PRS), and another which is the azimuthing podded drive system (AZIPOD). In order to calculate the performance characteristics of PRS and AZIPOD, which are lifting surface bodies, the propeller vortex theory is applied to calculate the forces acting on the propeller, assuming an infinitely bladed propeller. The panel method in the lifting body theory is adopted to calculate the forces acting on the rudder and steering system. Computed velocity components show good agreement with experimental measurements behind a propeller both with and without a rudder. Calculated thrust, torque and lift also show good agreement with the experiments. Computations are also given for an AZIPOD. Although our insight show that the numerical results of the hydrodynamic performance for the AZIPOD system are qualitatively good, it is recommended that it be examined with the experimental data.
-
Pages 415-424The performance of a grinding circuit in the Esfordi phosphate mineral processing plant, located in Yazd Province, Iran was evaluated. For this purpose, samples from different units including i) rod mill feed and product, ii) first hydrocyclone feed, overflow, underflow, iii) ball mill product, and iv) second hydrocyclone underflow were taken within 7 days for screen analyzing, solid percent and work index tests. From the test results, the work index of the ore was equal to 9.47kwh/t and d80 of the above samples were determined as17686.0, 274.3, 238.7, 100.9, 236.5, 206.4, 94.1 microns, respectively. In addition, the solid weight percent of the samples (except rod mill feed) were measured 55.6, 58.0, 83.6, 76.0, and 54.0 percent. According to the calculations, the reduction ratios of rod and ball mills were 64.65 and 1.15, which show high discrepancies from design values (23 and 7.5 for rod and ball mills). In the next step the diameters of the mill media were estimated. These were conducted at 12.5 and 3.5cm for rod and ball diameters, respectively. Therefore, increasing rod diameter from 8cm (current) to 12.5cm (estimated) could decrease the effective rod surface involved in breakage. This causes a reduction in the number of rod-particle impacts in a mill and results in decreasing the rod mill reduction ratio. In another way, by changing balls from 5cm (current) to 3.5cm (estimated), the breakage in the ball mill is increased and therefore its reduction ratio is higher. In addition, the residence time distribution of particles in rod and ball mills were measured using NaOH as a tracer in mill feeds and measuring pH in mill output in sequential times. The mean residence time of particles in rod and ball mills were equal to 16.68 (maximum 51) and 2.07 (maximum 20) minutes, respectively, which can be considered as one significant reason for the high and low reduction ratios in rod and ball mills.
-
Pages 425-436The high thickness of heads used in pressure vessels is always one of the main concerns of designers and manufacturers. A comprehensive analytical and experimental study has been conducted by the authors on all types of heads including torispherical heads (under external and internal pressure) to come up with a procedure to reduce their thicknesses using stiffening-rings. The result of the experiments and Finite Element Analysis (FEA) on torispherical heads with pressure on their concave side are presented in this paper. A method for determining the dimensions of the most suitable ring and its location on heads as well as its effect on the reduction of head thickness is addressed. The experimental results show good agreement with the analytical calculations and confirm that suitable stiffening-rings, in most cases, could considerably reduce head thicknesses.